- Molybdenum: mining and processing
Molybdenum can be found in a number of minerals, but only molybdenite is suitable for the industrial production of marketable molybdenum products. Molybdenite can occur as the sole mineralization in an ore body, but is usually associated with the sulphide minerals of other metals, mainly copper. Molybdenum mines are classified into three groups according to the minerals contained in the ore body and their quality:
- •Primary mines, where the extraction of molybdenite is the sole aim.
- •By-product mines, where the extraction of copper-bearing ores is the primary aim, and molybdenite extraction provides additional economic value.
- •Co-product mines, where both molybdenite and copper-bearing minerals are extracted.
- Roughly 40 percent of molybdenum comes from primary mines, with the other 60 percent a by-product of copper or, in some cases, tungsten.
- If the ore lies close to the surface, open-pit technology will be used, and if the ore lies deep underground, the underground method will be used.
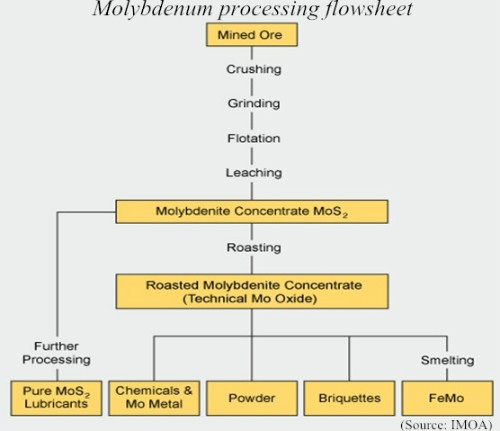
- Flotation
Once the ore has been crushed and ground, the metallic minerals are then separated from gangue minerals (or the molybdenum and copper from each other) by flotation processes, using a wide variety of reagents. The resulting MoS2 concentrate usually contains 85%~92% MoS2 and small amounts of copper (less than 0.5 percent) if the molybdenum is recovered as a by-product of copper. Further treatment by acid leaching can be used to dissolve impurities like copper and lead if necessary.
- Roasting
About 97 percent of MoS2 concentrate is converted into technical molybdic oxide (85~90% MoO3) to reach its commercial destination. Such conversion is usually carried out in multi-level hearth furnaces, in which molybdenite concentrates is fed from top to bottom against a current of heated air and gases blown from the bottom. Large rotary rakes move the molybdenite concentrate to promote the chemical reaction. Desulfurisation systems such as sulfuric acid plants or lime scrubbers remove sulfur dioxide from the effluent roaster gases. The resulting technical mo oxide typically contains a minimum of 57% molybdenum, and less than 0.1% sulfur.
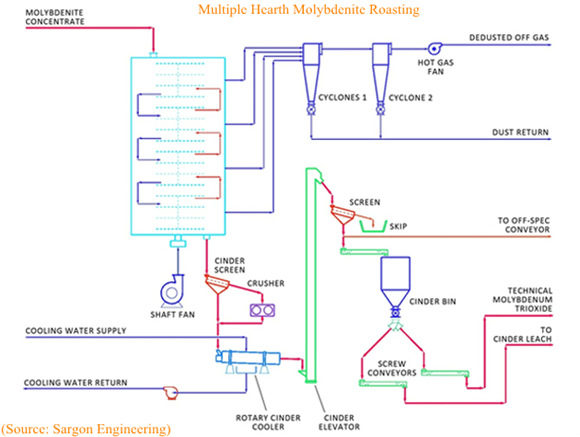
- Upgrading
- About 25% of the technical mo oxide produced worldwide is processed into a number of chemical products. Upgrading is performed by sublimation to produce pure MoO3 or by wet chemical processes to produce various pure molybdenum chemicals. MoO3 must be 99.95% pure in order to be suitable for the manufacture of ammonium molybdate (ADM) and sodium molybdate, which are starting materials for all sorts of molybdenum chemicals. Reacting chemically pure MoO3 with aqueous ammonia or sodium hydroxide obtains these compounds. Ammonium molybdate is used for the preparation of molybdenum chemicals and catalysts as well as metallic molybdenum powder.
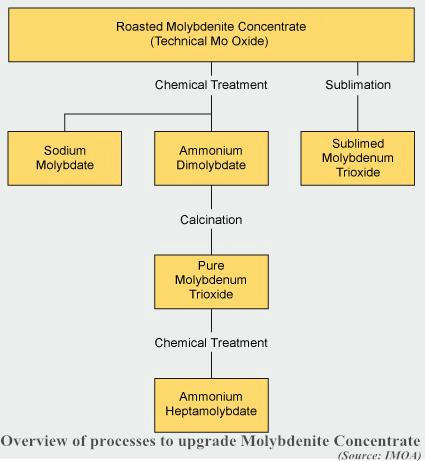
- Molybdenum metal production
- Metallic molybdenum is produced by hydrogen reduction of pure molybdenum trioxide (MoO3) or ammonium dimolybdate (ADM). The production is carried out in electrically heated tubes or muffle furnaces, into which hydrogen gas is introduced as a countercurrent against the feed. Usually there are two stages in which the MoO3 or ADM is first reduced to a dioxide and then to a metal powder.
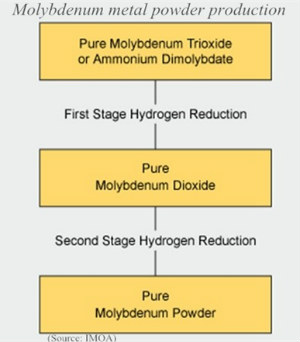
-
About us
Contact us
Make a suggestion
- Metalpedia is a non-profit website, aiming to broaden metal knowledge and provide extensive reference database to users. It provides users reliable information and knowledge to the greatest extent. If there is any copyright violation, please notify us through our contact details to delete such infringement content promptly.