Magnesium is the lightest of all light metal alloys and therefore is an excellent choice for engineering applications when weight is a critical design element. It is strong, has good heat dissipation, good damping and is readily available. Its properties make it easy to weld, forge, cast or machine. It can be alloyed with other metals, making them more beneficial. The use of pure magnesium is rare due to its volatility at high temperatures and it is extremely corrosive in wet environments. Therefore the use of magnesium alloys when designing aerospace and automotive parts is critical.
- Pure magnesium
- Burning magnesium produces white light. This makes it ideal for firework sparklers, flares and flash photography. It also functions as an agent to produce uranium out of salt. The element’s ions are necessary for every living organism. That is why magnesium salt is included in fertilizers and food. In many cases, magnesium bromide is utilized as a sedative. Magnesium is also used to remove sulfur from iron and steel.
- More about compounds
The element magnesium has numerous compounds. The most vital commercially are sulfates, carbonates, chlorides, hydroxides and oxides. These are used in textile processing, leather tanning, insulation, fertilizers, cosmetics and ceramics. The citrates of magnesia and magnesium hydroxide are used in medication. The element can interact with organic halides.
- Magnesium alloys
- Magnesium alloys are in use around the world in a variety of different applications. They are a preferred material when looking for weight reduction without compromising overall strength. The vibration damping capacity is also beneficial in applications in which the internal forces of high-speed components must be reduced.
- The most common applications are:
- •Aircraft and missile components
- •Aircraft engine mounts, control hinges, fuel tanks, wings
- •Automotive wheels, housings, transmission cases, engine blocks
- •Bicycles and other sporting equipment
- •Equipment for material handling
- •Ladders
- •Laptops, televisions, cell phones
- •Luggage
- •Portable power tools, chainsaws, hedge clippers, weed whackers
- •Printing and textile machinery
- •Steering wheels and columns, seat frames
- Magnesium alloys have also been used as a replacement for some engineering plastics due to their higher stiffness, high recycling capabilities and lower cost of production.
- Today's interest in magnesium alloys for automotive applications is based on the combination of high strength properties and low density. In automotive applications weight reduction will improve the performance of a vehicle by reducing the rolling resistance and energy is used in acceleration, thus reducing fuel consumption and, moreover, a reduction in the greenhouse gas CO2 can be achieved.
- In the 1920s magnesium began to make an appearance in the automotive industry. The light weight metal began to be used in racing car adding to their competitive edge. About a decade later, magnesium began to be used in commercial vehicles such as the Volkswagen Beetle which contained about 20kg (44.09lbs) of the material. Interest in using magnesium in automotive applications has increased over the past decade in response to the increasing environmental and legislative influences. Fuel efficiency, increased performance and sustainability are top-of-mind issues.
- The use of magnesium in vehicles can, and does, lower overall weight and improves each of these conditions. Many large automotive companies have already replaced steel and aluminum with magnesium in various parts of their products. Audi, DaimlerChrysler (Mercedes-Benz), Ford, Jaguar, Fiat and Kia Motors Corporation are just a few of these companies. Magnesium is currently being used in gearboxes, steering columns and driver’s air bag housings as well as in steering wheels, seat frames and fuel tank covers.
The use of magnesium in automotive applications can provide more than just weight savings. For many years, the desire to identify challenges, solutions, and opportunities regarding the use of magnesium in vehicles has been growing. Magnesium usage on the front end of a vehicle provides not just a lower overall mass for the car, but also allows for the shifting of the center of gravity towards the rear improving the car’s handling and turning capabilities. In addition, frequencies that reduce vibration and overall noise can be achieved through the tuning of magnesium parts. Steel components in vehicles can be replaced by a single cast piece of magnesium adding to the strength of the material and allowing for housings to be cast into place. This castability also requires less tooling and fewer gauges, which lowers manufacturing costs.
- According to the United States Automotive Materials Partnership (USAMP), it is estimated that by 2020, 350 lbs of magnesium will replace 500 lbs of steel and 130lbs of aluminum per vehicle, an overall weight reduction of 15%. In turn, this weight saving would lead to fuel savings of 9% to12% without any drastic changes in design. Considering the large number of vehicles produced worldwide, these weight savings could lead to a significant drop in the carbon dioxide released into the atmosphere, reducing its harmful impact on global warming. It is for this reason that magnesium is known as the green metal of the 21st century.
- Currently, multiple automobile parts can be made from magnesium alloys such as engine block, wheels, steering columns, seats, front consoles, and hoods .
Cars, vans and trucks are not the only vehicles that have incorporated magnesium in their designs. The aerospace industry has a long history of using the metal in many applications both civil and military. It is critical to lower the weight of air and space craft, as well as projectiles, if we are to achieve decreases in emissions and greater fuel efficiency. These changes will result in lower operational costs as well. Magnesium is an ideal material for use in these applications, due to limited continuing improvements on aluminum weight reduction, the high cost of fiber metal laminates, and the poor impact and damage properties of low density plastics when subjected to extreme temperatures. Magnesium can be found in the thrust reversers for the Boeing 737, 747, 757, and 767, as well as in engines and aircraft and helicopter transmission casings.
- Spacecraft and missiles also contain magnesium and its alloys. Lift-off weight reduction is of high importance in their design and a material is needed that can withstand the extreme conditions faced during their operation. Magnesium is capable of withstanding the extreme elevated temperatures, exposure to ozone and the impact of high energy particles and matter. It is also used in large quantity in intercontinental ballistic missiles such as Titan, Atlas and Agena.
In the 1st half of last century, magnesium was first introduced in the medical industry as an orthopedic biomaterial. There are many characteristics and properties that make magnesium a very attractive option for use in implants and similar applications. Other common implant materials have densities that range from 3.1-9.2g/cm3, whereas the density of natural bone is 1.8-2.1g/cm3 (112.37-131.10lb/ft3). Magnesium alloys are much more comparable, at a density of 1.74-2.0g/cm3 (108.62-lb/ft3). Magnesium is also much more akin to natural bone than other materials in regards to fracture toughness, elastic modulus and compressive yield strength. Not only does magnesium provide the mechanical and physical properties desirable in these applications, it also exhibits some special characteristics.
- Magnesium is found naturally as an ion in the human body equating to about one mole in a 155lb (70kg) person, half of which is stored within bone tissue. Magnesium within the body assists in metabolic reactions, has good biocompatibility, and is nontoxic. In addition, uncoated magnesium implants can be biodegradable in bodily fluids through corrosion, which eliminates the need for a further surgery to remove implants. Application of protective coatings can prevent corrosion issues in situations where a more permanent solution is needed. Research and testing of different alloys and formulas for protective finishes is currently in progress with the aim of increasing the array of ways in which magnesium can be used in medical applications.
- In the current market, small and portable electronics are trending upward. The demand for compact devices that can be easily transported is booming and magnesium is often a key component in meeting this demand. Many magnesium alloys being used to replace plastics are just as light, but they are much stronger and more durable. Magnesium is also better in regards to heat transfer and dissipation as well as its ability to shield electromagnetic and radio frequency interference. Many electronics require parts or casings with complex shapes which are possible with magnesium. Cameras, cell phones, laptops and portable media device housings are all common applications in addition to the arms of hard drives.
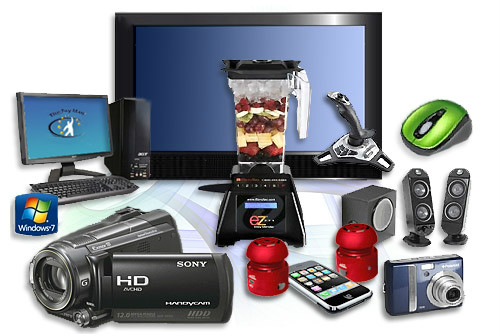
- Similar to its applications in other industries, magnesium is prized for use in sports equipment due to its light weight and impact resistance. Magnesium also has the ability to be formed into intricate shapes, which is ideal for use in golf clubs, tennis rackets and the handles of archery bows. The damping effects of the alloys also make it a good candidate for bicycle frames and the chassis of in-line skates, since the magnesium can absorb shock and vibration. This absorption allows cyclists to exert less energy and enjoy a smoother, more comfortable ride. Magnesium vaulting poles have also come into production as they have minimal twisting due to their high torsional strain resistance.
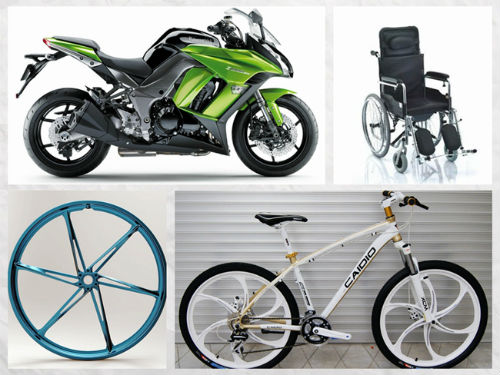
- Magnesium is utilized in optical and hand-held tool design. Wearers of spectacles often desire an aesthetically pleasing frame that is not felt during day-to-day wear but is sturdy enough to handle being removed and replaced throughout the day. Rifle scopes and binoculars must be stable in order to be effective and a light weight is also beneficial in their marketability. Magnesium allows for these design criteria to be met.
- Hand-held work tools and devices such chain saws, hand shears, hand drills, pneumatic nail guns and weed whackers are all perfect candidates for magnesium applications. The low density, comparative strength and vibration damping capabilities are all desirable characteristics in creation of handheld tools such as these.
- Magnesium has also found its way into small household appliances such as vacuums. By utilizing this material for a vacuum head, it will be light enough to easily move around as well as being dent resistant in normal use when coming in contact with furniture and other obstacles.
- As the inherent benefits of magnesium applications are further realized, the ways in which it can and will be used become numerous. Demand for sustainable, lightweight and recyclable materials is ever increasing with the push towards environmentally-conscious products, which can only be beneficial for the magnesium industry.
-
About us
Contact us
Make a suggestion
- Metalpedia is a non-profit website, aiming to broaden metal knowledge and provide extensive reference database to users. It provides users reliable information and knowledge to the greatest extent. If there is any copyright violation, please notify us through our contact details to delete such infringement content promptly.