- Magnesium is found in solution in sea-water (about 1.3 kg m-3 magnesium) and in natural brines. It is also found extensively in the ores magnesite (MgCO3) and dolomite (MgCO3.CaCO3). Both of the two types of resources can be used as raw materials to manufacture magnesium metal.
- Magnesium is principally produced by two methods:
- a) thermal reduction of magnesium oxide
- b) electrolysis of magnesium chloride
- Before the expansion of production in China, electrolysis was the more common method of production in countries where electrical energy is produced relatively cheaply. Most Chinese plants, however, use an updated version of the thermal reduction process originally developed in Canada in the 1940s to boost production during World War II (the 'Pidgeon Process').
- Dolomite is normally treated by the thermic method: this consists of reducing magnesium oxide, produced by calcining the dolomite raw material, with ferrosilicon to produce metallic magnesium and a calcium iron silicate slag.
- Step 1: Dolomite ore is crushed and heated in a kiln to produce a mixture of magnesium and calcium oxides, a process known as calcining:

- Step 2: The next step is reduction of the magnesium oxide. The reducing agent is ferrosilicon (an alloy of iron and silicon) which is made by heating sand with coke and scraps iron, and typically contains about 80% silicon.
- Step 3: The oxides are mixed with crushed ferrosilicon, and made into briquettes for loading into the reactor. Alumina may also be added to reduce the melting point of the slag. The reaction is carried out at 1500 - 1800 K under very low pressure, close to vacuum. Under these conditions the magnesium is produced as a vapour which is condensed by cooling to about 1100 K in steel-lined condensers, and then removed and cast into ingots:

- Step 4: The forward reaction is endothermic and the position of equilibrium is in favour of magnesium oxide. However, by removing the magnesium vapour as it is produced, the reaction goes to completion. The silica combines with calcium oxide to form the molten slag, calcium silicate:

- The process gives magnesium with up to 99.99% purity, slightly higher than from the electrolytic processes.
- Used to treat magnesite, serpentine, seawater magnesia and brines from carnallite and lake waters, the electrolytic process is usually the preferred choice outside China.
- The process involves two stages:
- i) production of pure magnesium chloride from sea water or brine
- ii) electrolysis of fused magnesium chloride
- (i) Production of pure magnesium chloride from sea water or brine
- Where sea-water is the raw material, it is treated with dolomite which has been converted to mixed oxides by heating to a high temperature. Magnesium hydroxide precipitates, while calcium hydroxide remains in solution. Magnesium hydroxide is filtered off and on heating readily forms the pure the oxide.
- Conversion to magnesium chloride is achieved by heating the oxide, mixed with carbon, in a stream of chlorine at a high temperature in an electric furnace (Figure 1).
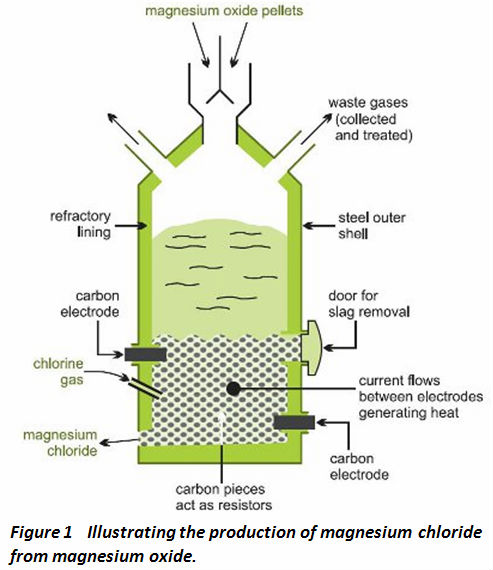
- Several reactions occur:
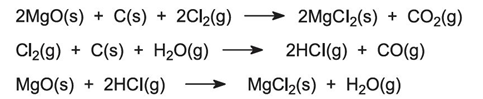
- Where magnesium chloride-rich brines are the source of magnesium, the solution is treated for removal of various impurities and the remaining magnesium chloride solution concentrated by evaporation in several stages.
- The last stage of dehydration has to be carried out in the presence of hydrogen chloride gas to avoid hydrolysis of the magnesium chloride:

- A new process is under development using magnesite. Small pieces of the ore are converted directly to molten magnesium chloride by heating with chlorine in an electric furnace in the presence of carbon monoxide.
- (ii) The electrolysis of fused magnesium chloride
- The resulting anhydrous magnesium chloride is fed continuously into electrolytic cells (Figure 2) which are hot enough to melt it.
- On electrolysis, magnesium and chlorine are produced:
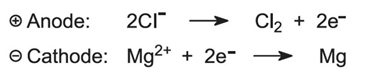
- The molten metal is removed and cast into ingots. The chlorine gas is recycled to the chlorination furnace.
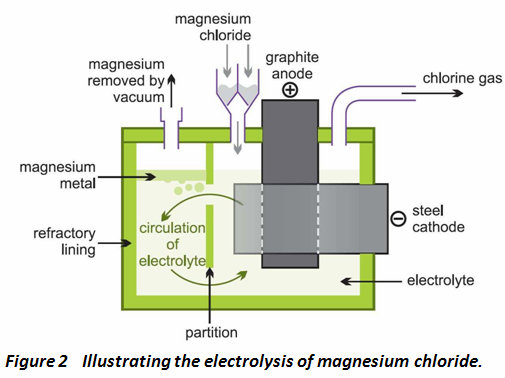
-
About us
Contact us
Make a suggestion
- Metalpedia is a non-profit website, aiming to broaden metal knowledge and provide extensive reference database to users. It provides users reliable information and knowledge to the greatest extent. If there is any copyright violation, please notify us through our contact details to delete such infringement content promptly.