- Titanium has been traditionally used as a lightweight, extremely strong and exceedingly corrosion-resistant material in aircraft, electric power plants, seawater desalination plants, and heat exchangers. More recently, it has found increasing applications in consumer products, sporting goods and information technology (IT) equipment by making use of its aesthetic surface appearance and luxurious feel.
Thousands of titanium alloys have been developed and these can be grouped into four main categories. Their properties depend on their basic chemical structure and the way they are manipulated during manufacture. Some elements used for making alloys include aluminum, molybdenum, cobalt, zirconium, tin and vanadium. Alpha phase alloys have the lowest strength but are formable and weldable. Alpha plus beta alloys have high strength. Near alpha alloys have medium strength but have good creep resistance. Beta phase alloys have the highest strength of any titanium alloys but they also lack ductility.
- There is a difference between countries on titanium applications. While aerospace accounts for half of the titanium demand in the US, Europe and Russia, industrial applications, particularly in chemical plants, dominate in Asia. These differentiated markets will continue to be the main demand drivers behind a growth of 4.6%py (in the past year) through to 2018.
The aerospace industry is the largest user of titanium products. It is a useful material for this industry because of its high strength to weight ratio and high temperature properties. Titanium is typically used for airplane parts and fasteners. These same properties make titanium useful for the production of gas turbine engines while it is also used for other parts such as the compressor blades, casings, engine cowlings and heat shields.
- The expansion in use of titanium within the aerospace market can be attributed to several factors, including the demand for newer aircraft designs with increased CFRP (carbon fiber reinforced polymer [or plastic]) composition. By sharing the same thermal expansion rates as many popular composite materials, titanium is highly favored as a composite interface material.
- The new Boeing 787 Dreamliner is estimated to use 15 percent titanium by weight, 5 percent more than steel and is surely the exemplar for the increased use of titanium in commercial aircraft manufacturing. Increased titanium use in this aircraft directly corresponds with that of composite components based on the materials’ compatibility. The rise in composite design, construction and use is a strong indicator of additional increases in titanium part production.
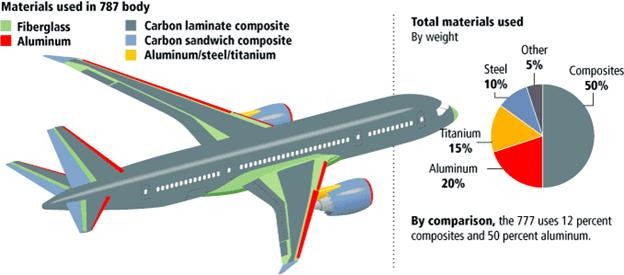
- Current industry projections for titanium indicate a 40 percent increase in demand by 2015. Anticipating this growth, many major producers of titanium have announced plans to increase their production capacities.
- Military aircraft
Titanium has been used in aircraft for nearly 60 years now, especially in military aircraft. Forty-two percent of the structural weight of the Lockheed Martin F22 Raptor, which entered service in the US at the end of 2005, consists of titanium. And even back in the ‘60s, some 93 percent of the Lockheed SR-71 Blackbird’s structural weight consisted of titanium alloys. It is also used in the Lockheed Martin JSF (accounting for around a third of the aircraft by weight), and in the Airbus A350 and A380 commercial airliners.
- The importance of titanium in the aerospace industry cannot be overstated. According to the latest figures from the US Geological Survey, in 2012, some 72 percent of titanium metal consumed in the US was used in aerospace applications, with the remaining 28 percent being used in “armor, chemical processing, marine, medical, power generation, sporting goods, and other nonaerospace applications.”
- Globally, as the English metal research house Roskill Information Services says in an overview of its forthcoming report on the metal (“Titanium Metal: Market Outlook to 2018”), with the increased use of composites, particularly carbon-compatible reinforced polymers (CFRP) in the manufacture of large passenger aircraft: “titanium’s position as a key material in the aerospace industry is assured and growing.”
- People have been developing using the ocean resource since the technology allows us to do it and the land resource is getting exhausted. Titanium is appealing for ocean engineering applications because of its excellent corrosion resistance feature. Therefore a great many of titanium products have been applied to the desalination of sea water, as well as for vessels and exploration of ocean resources.
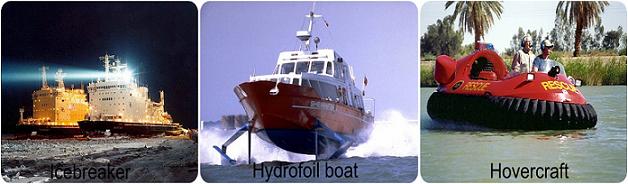
- As early as the 1960s, China had begun carrying out application research into the use of titanium in vessels. With much effort, a sound system of vessel grade titanium was established. Titanium enjoys unique advantages when applied to vessels and the marine industry. Submarines, bathyvessels, atomic icebreakers, hydrofoils, hovercrafts, minesweepers and propellers all have titanium in them.
- Though China has a sound system for vessel grade titanium and the titanium used on vessels is growing, many key technologies haven’t yet been grasped due to the lack of cooperation between research organizations, material research institutions and vessel companies.
- In Russia, titanium consumption on vessels has reached 15%-20%, meaning the titanium market will be boosted dramatically, reaching hundreds of billions of dollars in market value. Oil exploration and exploitation will be the next potential market for titanium. Just one offshore oil drilling platform requires 1,500-2,000 tonnes of titanium. China plans to construct 70 platforms in the next 3-5 years, and consumption of titanium will reach 140 thousand tonnes. In addition, China has a great need for desalination and coastal power stations, and if cost reductions and quality improvements can be achieved, the titanium market’s prospects will be very bright.
The list of titanium’s benefits is lengthy. This makes it incredibly useful for a number of different industries, including the automotive, aerospace and architectural worlds. But because titanium resists corrosion, is biocompatible and has an innate ability to join with human bone, it has become a staple of the medical field, as well. From surgical titanium instruments to orthopedic titanium rods, pins and plates, medical and dental titanium has truly become the fundamental material used in medicine.
- Common titanium applications in terms of medical industry:
• Hip and knee joints
- • Bone screws
- • Bone plates
- • Dental implants
- • Surgical devices
- • Pacemaker cases
- • Spectacle frames
- • Heart valves
- • Pharmaceutical equipment
- • Wheelchairs
- It is expected that uses for titanium within the biomedical industry will only continue to grow in the coming years. With the baby-boomer demographic continuing to age and our health industry pushing people to live more active lives, it’s only logical that the medical industry will continue researching new and innovative uses for this popular metal alloy. And with healthcare reform a current major issue, titanium’s cost-efficiency adds even more appeal to those looking to cut healthcare costs.
- In the field of automobiles, titanium found its first application within the engine parts of racing cars early in the 1980s. Since then, the range of applications for titanium has expanded to include its application in the muffler systems of super short-type bikes and limited models of high-performance cars.
- Because of its great strength and low density, combined with virtual immunity to corrosion in the automotive environment, titanium offers many attractions for use in automobile applications. Despite its advantages, however, titanium hasn’t yet found a widespread use because the automotive industry is very price sensitive. The cost of titanium is relatively higher than that for steel or aluminum alloys. However, for some applications titanium is attracting great interest.
Production passenger automobile components which could benefit from using of titanium include engine valves, connecting rods and valve spring retainers, as well as valve springs. However, until recently the use of titanium in the family automobile had not progressed beyond the prototyped stage because of the high cost of titanium compared to competing materials. There are two major obstacles that must be overcome if titanium is to be used in high-volume production.
- According to a survey, in China, titanium is primarily used in chemical applications such as heat-exchanger (57%), titanium anode (20%), titanium container (16%) and others (7%). In the chemical industry, chlor-alkali and sodium carbonate are major consumers of titanium.
- Titanium distributors are quickly finding more widespread uses for titanium tubing in recreational products, including sports equipment such as bicycles, golf clubs and tennis racquets. Titanium sheet and wire is now an attractive alternative to other special metals used in the jewelry industry, particularly in wedding jewelry.
- In 2008, titanium consumption on sports equipment accounted for 13% of the total in China, with golf heads and golf clubs alone consuming over 1,000 tonnes. Bicycles made with titanium alloy frames are also catching on, and there are nearly 50 companies currently doing business in the titanium bicycles field. For a long time the US has been the biggest titanium bicycle producer and consumer. Spectacle frames are another famous application of titanium due to its extraordinary lightness and less tendency to be less allergenic to skin. Besides, after anodic treatment, titanium can be colorful which makes it even more popular as a frame material.
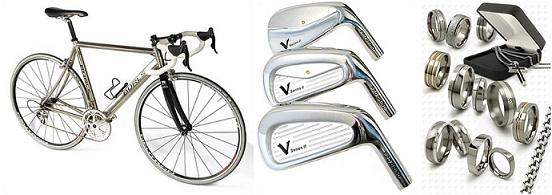
- With ever advancing technologies, applications for titanium in daily life are expanding rapidly, but still, America and Japan are the leaders in this field.
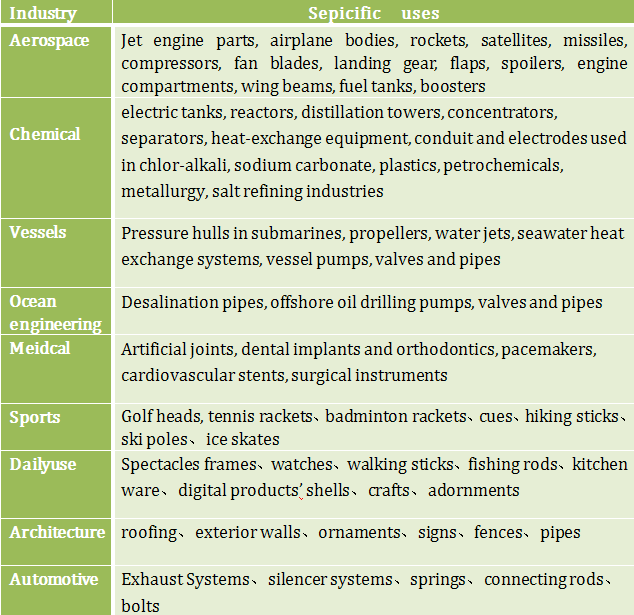
Titanium metal and TiO2 pigment are the two main products made from titanium minerals, and upon them large industries depend. First by far in terms of volume produced is microcrystalline TiO2 for white pigment. Because of the extremely high refractive index of TiO2 as rutile (2.6 to 2.9, or higher than diamond), it is the chief opacifying pigment used in paint and other products such as plastics and paper, not only for white color but for quite a range of colors. Titanium dioxide pigment commonly forms more than 20 percent by weight of some paints. The pigment industry consumes more than 90 percent of all titanium minerals mined.
The product ranked second by volume, though perhaps not in importance, is titanium metal. The high strength-to-weight ratios and resistance to corrosion and high temperatures of titanium metal and titanium-based alloys make them important ingredients in many industries. Most important is the aircraft industry, where the use of titanium has been growing for more than 30 years, to the point that the current generation of commercial airliners can contain 30 percent titanium by weight. Another trend during recent times has been a diversification of titanium-metal uses in other industries. Many industries take advantage of titanium’s corrosion resistance, as in heat exchangers and desalination plants.
- 1. Titanium sponge
- 2. Titanium dioxide pigment
-
About us
Contact us
Make a suggestion
- Metalpedia is a non-profit website, aiming to broaden metal knowledge and provide extensive reference database to users. It provides users reliable information and knowledge to the greatest extent. If there is any copyright violation, please notify us through our contact details to delete such infringement content promptly.