- Tungsten: extraction and processing
The mining methods used depends on the physical and chemical properties of the mineral, tonnage and grade, the physical form in which it occurs, the geometry and the depth of the orebody. The common extraction methods are surface (or open pit) mining and sub-surface (or underground) mining, or a combination of both.
- Surface mining
- Open-pit mining is used if near-surface ore body is massive or when it occurs in steeply-dipping lode(s), sheeted vein systems, pipes, or makes up the bulk of the country rock as in disseminated or prophyry-style deposits. The whole ore body is mined with no overburden being put back into the void during the extraction operation.
- Some placer deposits are amenable to strip mining or dredging operations. In strip mining the overburden is removed and deposited in the hole left from the excavation of the previous strip or panel and the ore can be simply dug out. Hydraulic mining is commonly used in reclamation of old mine tailings that still contain payable values of tungsten.
- Underground mining
Underground mining is preferred when surface mining is, or becomes, expensive. A major factor in the decision to mine underground is the ratio of waste to ore (strip ratio). Once this ratio becomes large, surface mining is no longer economic. Underground access is through an adit (an entrance to a mine which is horizontal or nearly horizontal), a shaft or a decline. Ore is mined in stopes (the void created by extracting the ore) on a number of roughly horizontal levels at various depths below the surface.
- Concentrates (Primary Tungsten Sources)
- Modern processing methods dissolve scheelite and wolframite concentrates by an alkaline pressure digestion, using either a soda or a concentrated NaOH solution. The sodium tungstate solution obtained is purified by precipitation and filtration, before it is converted into an ammonium tungstate solution. This stage is carried out exclusively by solvent extraction or ion exchange resins. Finally, high purity Ammonium-Paratungstate (APT) is obtained by crystallization.
- Wolframite concentrates can also be smelted directly with charcoal or coke in an electric arc furnace to produce ferrotungsten (FeW) which is used as alloying material in steel production. Pure scheelite concentrate may also be added directly to molten steel.
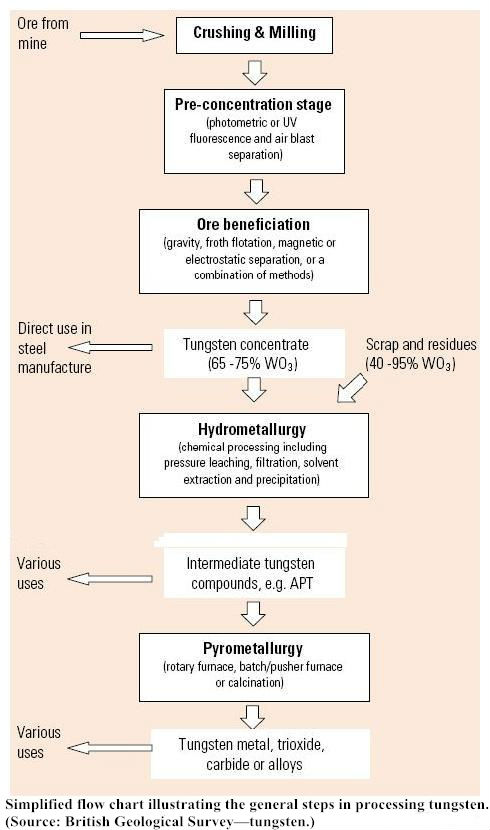
- Scrap (Secondary Tungsten Sources)
- Tungsten scrap is a very valuable raw material due to its high tungsten content in comparison to ore.
- Contaminated cemented carbide scrap, turnings, grindings and powder scrap are oxidized and chemically processed to APT in a way similar to that used for the processing of tungsten ores. If present, cobalt, tantalum and niobium are recovered in separate processing lines. Other tungsten containing scrap and residues might require a modified process.
- Clean cemented carbide inserts and compacts are converted to powder by the zinc process (treatment with molten zinc which is dissolved in the cobalt phase and is then distilled off, leaving a spongy material which is easily crushed). This powder is added back to the manufacture of ready-to-press powder. By this process, not only tungsten carbide but also cobalt, tantalum carbide and other carbides are recycled.
- Recycling of tungsten in high speed steel is high, and a typical melt contains 60% to 70% scrap, including internally generated scrap.
On the other hand, recycling in such applications as lamp filaments, welding electrodes and chemical uses is low.
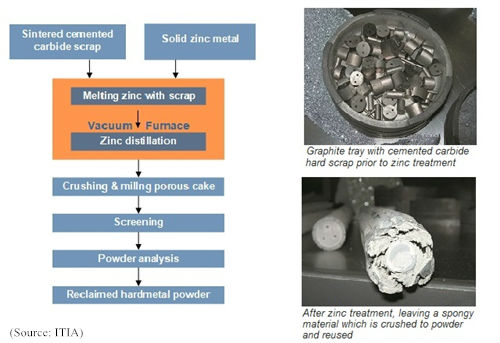
-
About us
Contact us
Make a suggestion
- Metalpedia is a non-profit website, aiming to broaden metal knowledge and provide extensive reference database to users. It provides users reliable information and knowledge to the greatest extent. If there is any copyright violation, please notify us through our contact details to delete such infringement content promptly.