- 80% of zinc mines are underground, 8% are of the open pit type and the remainder is a combination of both. However, in terms of production volume, open pit mines account for as much as 15%, underground mines produce 64% and 21% of mine production comes from the combined underground and open pit mining.
- Zinc is found in the earth’s crust primarily as zinc sulfide (ZnS). Rarely is the ore, as mined, rich enough to be used directly by smelters; it needs to be concentrated. Zinc ores contain 5-15% zinc. To concentrate the ore, it is first crushed and then ground to enable optimal separation from the other minerals. Typically, a zinc concentrate contains about 55% of zinc with some copper, lead and iron. Zinc concentration is usually done at the mine site to keep transport costs to smelters as low as possible.
- Zinc smelting is the process of converting zinc concentrates (ores that contain zinc) into pure zinc. The most common zinc concentrate processed is zinc sulfide, which is obtained by concentrating sphalerite using the froth flotation method. Secondary (recycled) zinc material, such as zinc oxide, is also processed with the zinc sulfide. Approximately 30% of all zinc produced is from recycled sources.
- There are two methods of smelting zinc: the pyrometallurgical process and the hydrometallurgical process (over 90% of hydrometallurgical process is in electrolytic plants using electrolysis process). Both methods are still used. Both of these processes have the same first step: roasting.
- Roasting is a process of oxidizing zinc sulfide concentrates at high temperatures into an impure zinc oxide, called "Zinc Calcine". The chemical reactions taking place during the process are:
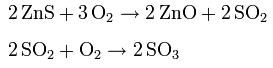
- The process of roasting varies based on the type of roaster used. There are three types of roasters: multiple-hearth, suspension, and fluidized-bed.
- Today over 90% zinc is produced hydrometallurgically in electrolytic plants.
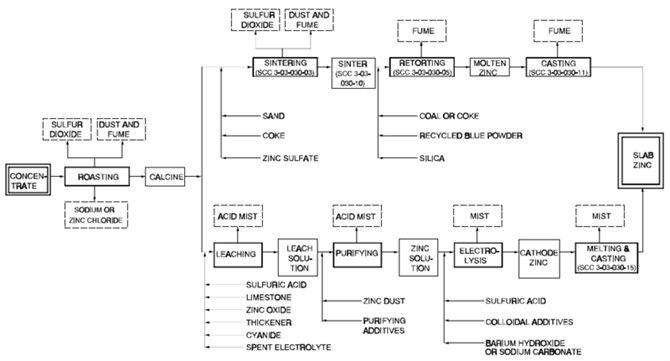
- Electrolysis process
- The electrolysis process, also known as the hydrometallurgical process, Roast-Leach-Electrowin (RLE) process, or electrolytic process, is more widely used than the pyrometallurgical processes.
- The electrolysis process consists of 4 steps: leaching, purification, electrolysis, and melting and casting.
- Leaching
- The basic leaching chemical formula that drives this process is:

- Purification
- The purification process utilizes the cementation process to further purify the zinc. It uses zinc dust and steam to remove copper, cadmium, cobalt, and nickel, which would interfere with the electrolysis process.
- Electrolysis
- Zinc is extracted from the purified zinc sulfate solution by electrowinning, which is a specialized form of electrolysis. The process works by passing an electric current through the solution in a series of cells. This causes the zinc to deposit on the cathodes (aluminium sheets) and oxygen to form at the anodes. Sulfuric acid is also formed in the process and reused in the leaching process. Every 24 to 48 hours, each cell is shut down, the zinc-coated cathodes are removed and rinsed, and the zinc is mechanically stripped from the aluminium plates.
- Electrolytic zinc smelters contain as many as several hundred cells. A portion of the electrical energy is converted into heat, which increases the temperature of the electrolyte. Electrolytic cells operate at temperature ranges from 30 to 35 °C (86 to 95 °F) and at atmospheric pressure. A portion of the electrolyte is continuously circulated through the cooling towers both to cool and concentrate the electrolyte through evaporation of water. The cooled and concentrated electrolyte is then recycled to the cells. This process accounts for approximately one-third of all the energy usage when smelting zinc.
- There are two common processes for electrowinning the metal: the low current density process, and the Tainton high current density process. The former uses a 10% sulfuric acid solution as the electrolyte, with current density of 270–325 amperes per square meter. The latter uses 22–28% sulfuric acid solution as the electrolyte with a current density of about 1,000 amperes per square metre. The latter gives better purity and has higher production capacity per volume of electrolyte, but has the disadvantage of running hotter and being more corrosive to the vessel in which it is done. In either of the electrolytic processes, each metric ton of zinc production expends about 3,900 kW•h (14 GJ) of electric power.
- Melting and casting
- The final step is to melt the cathodes in an induction furnace. It is then either cast into pure zinc (99.995% pure) ingots or alloyed and cast into ingots.
- There are also several pyrometallurgical processes that reduce zinc oxide using carbon, then distil the metallic zinc from the resulting mix in an atmosphere of carbon monoxide. The major downfall of any of the pyrometallurgical process is that it is only 98% pure; a standard composition is 1.3% lead, 0.2% cadmium, 0.03% iron, and 98.5% zinc. This may be pure enough for galvanization, but not enough for die casting alloys, which requires special high-grade zinc (99.995% pure). In order to reach this purity the zinc must be refined. The four types of commercial pyrometallurgical processes are the St. Joseph Minerals Corporation's (electrothermic) process, the blast furnaceprocess, the New Jersey Zinc continuous vertical-retort process, and the Belgian-type horizontal retort process.
- St. Joseph Mineral Company (electrothermic) process
- This process was developed by the St. Joseph Mineral Company in 1930, and is the only pyrometallurgical process still used in the US to smelt zinc. The advantage of this system is that it is able to smelt a wide variety of zinc-bearing materials, including electric arc furnace dust. The disadvantage of this process is that it is less efficient than the electrolysis process.
- The process begins with a downdraft sintering operation. The sinter, which is a mixture of roaster calcine and EAF calcine, is loaded onto a gate type conveyor and then combustions gases are pumped through the sinter. The carbon in the combustion gases react with some the impurities, such as lead, cadmium, and halides. These impurities are driven off into filtration bags. The sinter after this process, called product sinter, usually has a composition of 48% zinc, 8% iron, 5% aluminium, 4% silicon, 2.5% calcium, and smaller quantities of magnesium, lead, and other metals. The sinter product is then charged with coke into an electric retort furnace. A pair of graphite electrodes from the top and bottom furnace produce current flow through the mixture. The coke provides electrical resistance to the mixture in order to heat the mixture to 1,400 °C (2,550 °F) and produce carbon monoxide. These conditions allow for the following chemical reaction to occur:

- The zinc vapour and carbon dioxide pass to a vacuum condenser, where zinc is recovered by bubbling through a molten zinc bath. Over 95% of the zinc vapour leaving the retort is condensed to liquid zinc. The carbon dioxide is regenerated with carbon, and the carbon monoxide is recycled back to the retort furnace.
- Blast furnace process (Imperial Smelting Process)
- This process was developed by the National Smelting Company at Avonmouth Docks, England, in order to increase production, increase efficiency, and decrease labour and maintenance costs. L. J. Derham proposed using a spray of molten lead droplets to rapidly chill and absorb the zinc vapour, despite the high concentration of carbon dioxide. The mixture is then cooled, where the zinc separates from the lead. The first plant using this design opened up in 1950. One of the advantages of this process is that it can co-produce lead bullion and copper dross. In 1990, it accounted for 12% of the world's zinc production.
- The process starts by charging solid sinter and heated coke into the top of the blast furnace. Preheated air at 190 to 1,050 °C (370 to 1,920 °F) is blown into the bottom of the furnace. Zinc vapour and sulfides leave through the top and enter the condenser. Slag and lead collect at the bottom of the furnace and are tapped off regularly. The zinc is scrubbed from the vapour in the condenser via liquid lead. The liquid zinc is separated from the lead in the cooling circuit. Approximately 5,000 metric tons (5,500 short tons) of lead are required each year for this process, however this process recovers 25% more lead from the starting ores than other processes.
- The IS process is an energy-intensive process and thus became very expensive following the rise of energy prices. Today, Imperial Smelting furnaces are only in operation in China, India, Japan and Poland.
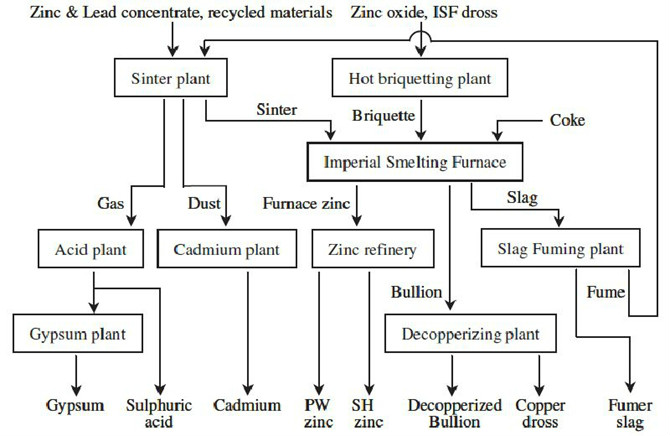
- New Jersey Zinc continuous vertical retort
- The New Jersey Zinc process is no longer used to produce primary zinc in the U.S., Europe and Japan, however it still is used to treat secondary operations. This process peaked in 1960, when it accounted for 5% of world zinc production. A modified version of this process is still used at Huludao, China, which produced 65,000 metric tons per year.
- This process begins by roasting concentrates that are mixed with coal and briquetted in two stages. The briquettes are then heated in anautogenous coker at 700 °C (1,292 °F) and then charged into the retort. There are three reasons to briquette the calcine: to ensure free downward movement of the charge; to permit heat transfer across a practical size cross-section; to allow adequate porosity for the passage of reduced zinc vapour to the top of the retort. The reduced zinc vapour that is collected at the top of the retort is then condensed to a liquid.
- Overpelt improved upon this design by using only one large condensation chamber, instead of many small ones, as it was originally designed. This allowed for the carbon monoxide to be recirculated into the furnaces for heating the retorts.
- This process was licensed to the Imperial Smelting Company (ISC), in Avonmouth, England, which had a large vertical retort (VR) plant in production for many years. It was used until the mid-1970s when it was superseded by the company's Imperial Smelting Furnace (ISF) plant. The VR plant was demolished in 1975.
- Belgian-type horizontal retort process
- This process was the main process used in Britain from the mid-19th century until 1951. The process was very inefficient as it was designed as a small scale batch operation. Each retort only produced 40 kilograms (88 lb), so companies would put them together in banks and used one large gas burner to heat all of them. The Belgian process requires redistillation to remove impurities of lead, cadmium, iron, copper, and arsenic.
- Source: Zinc smelting--Wikipedia; 12.7 Zinc Smelting--EPA; Zinc Production-From Ore to Metal--International Zinc Association
-
About us
Contact us
Make a suggestion
- Metalpedia is a non-profit website, aiming to broaden metal knowledge and provide extensive reference database to users. It provides users reliable information and knowledge to the greatest extent. If there is any copyright violation, please notify us through our contact details to delete such infringement content promptly.