- Rare earths: industrial technology
- As this group has 17 kinds of elements, the applications of rare earth elements are diversified: compounds from chloride 46% purity and 99.9999% of single rare earth oxides. The products are various. Details of their separation methods and smelting process are as follows.
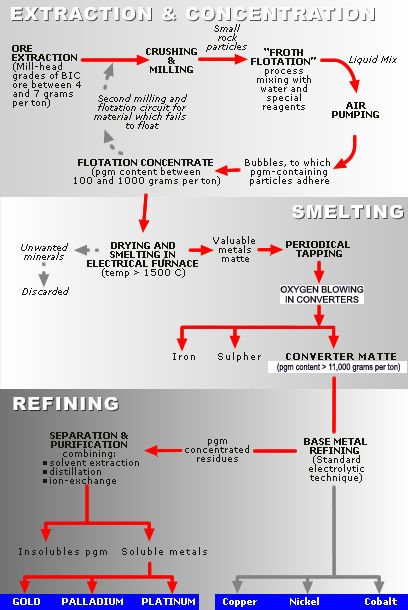
- Source: http://www.googlelunarxprize.org/teams/team-phoenicia/blog/lunar-mining-part-two-the-standard-terrestrial-process
Beneficiation is a machining process for enrichment of useful minerals, removing harmful impurities, and separating useful minerals from gangue minerals by using the various properties of different minerals, adopting different beneficiation methods with their own techniques and equipment. Usually, beneficiation of rare earth elements adopts the technological process known as the flotation method and is often accompanied by various combinations of gravity separation and magnetic separation.
The rare earth elements exist in the form of carbonates, fluorides, phosphates, oxides or silicates in rare earth ore concentrate. Usually, they are poorly soluble in water. After a variety of chemical changes, they are transformed into compounds which are soluble in water or mineral acid. Then after dissolution, separation, purification, concentration or burning processes, they are made into all kinds of mixed rare earth compounds such as mixed rare earth chloride. These rare earth compounds will be the raw materials for products or separation of single rare earth elements. The above process is called the concentrate decomposition method or pretreatment.
- There are many methods to concentrate decomposition. Generally it can be classified into three categories: acid, alkaline and chlorinated decomposition. Acid decomposition is divided into hydrochloric acid decomposition, sulfuric acid decomposition and hydrofluoric acid decomposition, for example. Alkaline decomposition is divided into decomposition of sodium hydroxide and sodium hydroxide melting or the soda roasting method. Generally, the choice of suitable technological process is based on many characteristics, including the type and grade of concentrate, product plan, facilitation of recycling and comprehensive utilization of rare earth elements, labor hygiene and environmental protection, economic and reasonable factors, etc.
- Currently, nearly 200 kinds of rare earth element minerals have been discovered. However, because they are rare and are not well integrated with independent industrial mining ore deposits, so far only a few independent germanium, selenium or tellurium ores have been found and usually the scale of the ore deposit is not large.
There are two kinds of rare earth smelting method, pyrometallurgy and hydrometallurgy.
- Hydrometallurgy
- Hydrometallurgy is a general process for industrial separation of high purity single rare earth elements. This process is complex and the resulting products with high purity are widely used in various fields.
- Pyrometallurgy
- The pyrometallurgy process is relatively easy compared to hydrometallurgy, which has higher productivity. Pyrometallurgy of rare earths mainly covers the silicothermic process for preparing rare earth alloys, the fused salt electrolysis process for preparing rare earth elements or alloys and metallothermics for preparing rare earth alloys. The common feature of these methods of pyrometallurgy is that they are all carried out under conditions of high temperature.
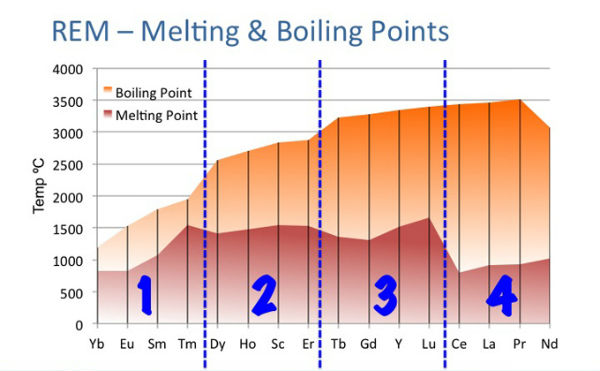
- Source: https://www.ameslab.gov/mpc/ames-process-rare-earth-metals
- Rare earth carbonate and rare earth chloride are the main primary products in the rare earth industry, and generally speaking, there are currently two main processes for producing these two products. One is concentrated sulfuric acid roasting, the other is the caustic soda method, hereinafter referred to as the alkaline process.
- In addition to the occurrence of the rare-earth elements in nature in a variety of rare earth mines, a considerable proportion of REE come from the symbiosis with apatite and phosphate rock ores. The total reserves of phosphorite ore in the world are about 100 billion tonnes, while their average content of REE is 0.05%. It is estimated that the total reserves of rare earth elements which come from the symbiosis with phosphate rock ore are 50 million tonnes. According to each REE’s characteristics, many kinds of collecting process have been studied at home and abroad. As we have mentioned, generally the processes can be classified into wet and hot. The wet method can itself be classified into nitric acid, hydrochloric acid and sulfuric acid methods. The recovery rate of the hot method can reach up to 60%.
- With the use of phosphate rock resources, the major focus has been turning towards the development of low quality phosphate rock. Sulfuric acid phosphoric acid by wet process has become the mainstream phosphorous chemical method, and collecting rare earth via wet-process phosphoric acid sulfate recycling has become a research focus. In the acid wet phosphoric acid production process, by controlling the enrichment of rare earth elements in the phosphoric acid, then adopting the organic solvent extraction process, the advantages are more obvious than with the method originally developed.
- As the physical and chemical properties of the 17 elements are similar and many impurity elements associated with REE come out along with them, the processes of their extraction are complicated. Commonly, there are three kinds of extraction technologies: the fractional step method, ion exchange method and solvent extraction method.
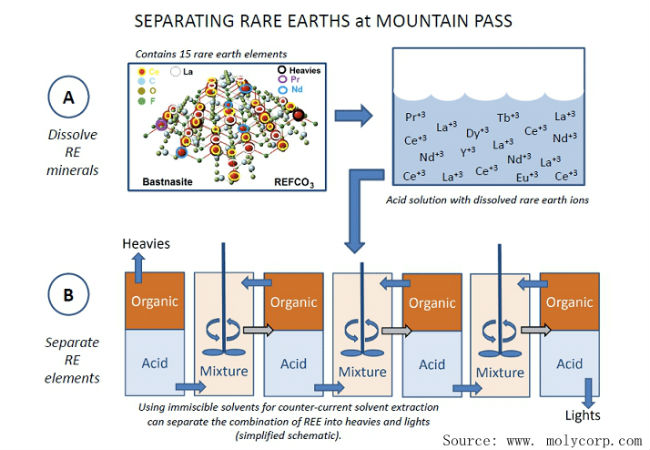
- Fractional step method
- The fractional step method is to extract and purify rare earth elements according to their compounds’ different solubility in the solvent. From yttrium (Y) to lutetium (Lu), all separations of the single rare earth element extracted from compounds of REE in nature were made with this method, including the discovery of radium by the Curies. The operational procedure of this method is complicated, and it took more than 100 years to extract all the 17 rare earth elements. As the extraction of one element needs to be repeated about 20,000 times, the workload for the chemist is pretty heavy. Therefore, this method is not suitable for large-scale production of single elements.
- Ion exchange method
- In order to analyse and make sure that the nuclear fission products contain rare earth elements and remove the rare earth elements from uranium and thorium, ion exchange chromatography (the ion exchange method) was arrived at successfully after some study. This method was then used for the separation of rare earth elements. The advantage of this method was that it could separate multiple elements with a single operation and the products were of high purity. However, it could not process continuously and took a long time for each operation, while some other procedures may add more cost. Thus, nowadays this method has been replaced by solvent extraction as the main separation method. But when high purity products are needed for single elements, this method is still needed for their extraction.
- Solvent extraction method
- The solvent extraction method is used to extract the products from an aqueous solution based on non-miscibility by using organic solvents. It is a kind of substance from a liquid transferred to another mass transfer process of the liquid phase. This method was first used in petrochemicals, organic chemistry, medicinal chemistry and analytical chemistry. Meanwhile, with the development of atomic energy science and technology and to meet the needs of super purity products and rare earth elements, , the solvent extraction method has improved greatly over the past forty years in the nuclear fuel and rare metallurgical industries. In China, study of the theory of extraction, the silicon-containing polymers of the new extractant and the separation process of rare earth extraction have reached a very high level. Thanks to these great improvements and advantages, the solvent extraction method has gradually become the main method of separating large amounts of rare earth elements.
- Raw materials
Currently, the raw materials for producing rare earth elements are their chloride and fluoride.
- Molten salt electrolysis
- Industrial mass production on mixtures of rare earth metals generally employs the molten salt electrolysis method.
- Meanwhile, the electrolysis process includes two methods: chloride electrolysis and oxide electrolysis. Samarium, europium, ytterbium and thulium are usually extracted by the reduction distillation method, and other elements can be extracted by either the electrolysis method or the reduction method.
- Chloride electrolysis is the most common way to produce metal, particularly misch metal, which is easily worked, with lower cost and less investment. But the disadvantage is pollution of the environment by liberation of chlorine.
- Vacuum reduction
- As electrolysis can usually only be used in the preparation of general industrial rare earth metals, if high purity metal needs to be prepared, vacuum reduction will generally be the choice. This method can produce 13 kinds of single rare earth elements, the exceptions being samarium, europium, ytterbium and thulium.
-
About us
Contact us
Make a suggestion
- Metalpedia is a non-profit website, aiming to broaden metal knowledge and provide extensive reference database to users. It provides users reliable information and knowledge to the greatest extent. If there is any copyright violation, please notify us through our contact details to delete such infringement content promptly.